15 Preferred Thermoforming Materials For Plastic Shipping Trays
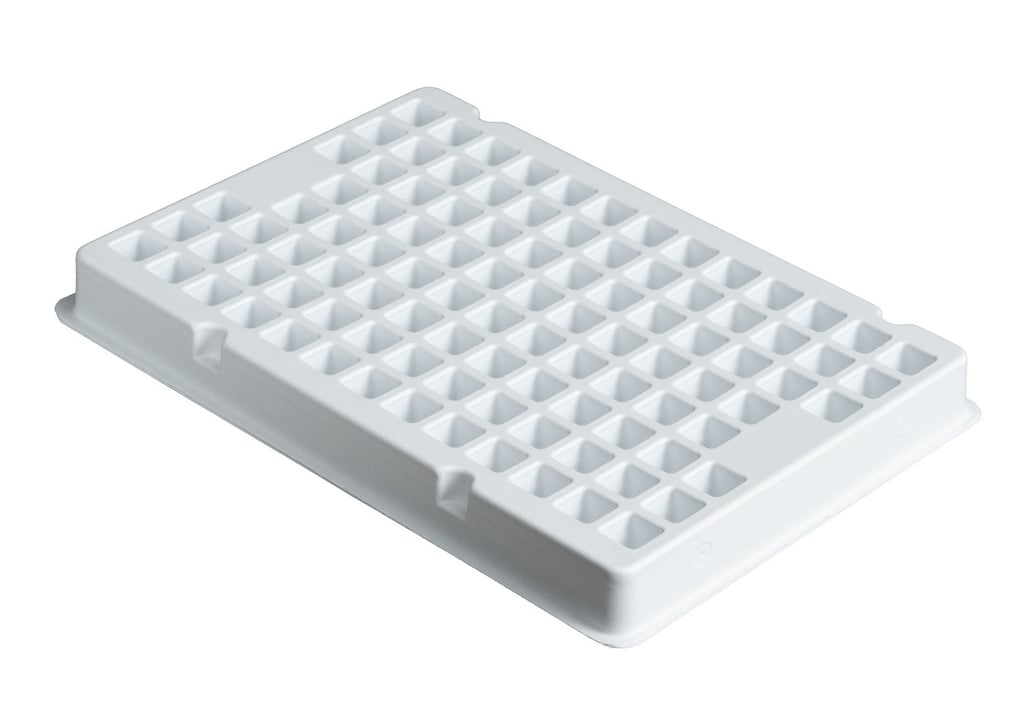
Not all plastics are usable in thermoforming, but there are an overwhelming number of options for thermoformed plastic shipping trays. Each of the materials listed in the chart below is considered a “thermoplastic” — a polymer resin that can be heated, reshaped, and cooled into a finished product. Flat sheets of these thermoplastics are transformed into trays when you soften them with heat and form them into one-sided molds by either vacuum forming or pressure forming.
The types of thermoforming materials you’ll choose for your shipping tray application will depend on your preferred material traits and the limitations of the products you’re shipping. Some of the materials here have only niche cases for use in shipping trays (like Polycarbonate or PC), while others are versatile all-purpose favorites (like High Impact Polystyrene or HIPS).
To help you make an informed decision, we’ve put together the following comparison table.
Types of Thermoforming Materials For Plastic Trays
Thermoforming Material |
Notable Properties |
Example Products |
Acrylonitrile Butadiene Styrene (ABS) |
|
|
Acrylic (“Plexiglass”) |
|
|
Cellulose Acetate |
|
|
Nylon |
|
|
Polystyrene (PS) |
|
|
High Impact Polystyrene (HIPS) |
|
|
Polycarbonate (PC) |
|
|
Polyetherimide (PEI) |
|
|
High Density Polyethylene (HDPE) |
|
|
High Molecular Weight Polyethylene (HMWPE) |
|
|
Polyethylene Terephthalate (PET) |
|
|
Polyethylene Terephthalate Glycol (PETG) |
|
|
Polypropylene (PP) |
|
|
Polyvinyl Chloride (PVC) |
|
|
Thermoplastic Olefin (TPO) |
|
|
These and other thermoplastics can be used in thermoforming to create custom-molded plastic goods like shipping trays, but they’re not all created equal. For most applications, materials like TPO and acrylic have traits that would make other options more cost-effective, easier to form, and ultimately more appropriate.
At Ready Made Plastic Trays, High Impact Polystyrene (HIPS) is one of our favorite thermoforming materials due to a great combination of traits: cost, customizability, durability, rigidity, and more. Most of our plastic shipping trays use HIPS, although we can certainly work with other materials as needed for your application. Connect with our team for more information on the material that would be right for your project.