Thermoforming vs. Injection Molding: Pros and Cons For Packaging Trays
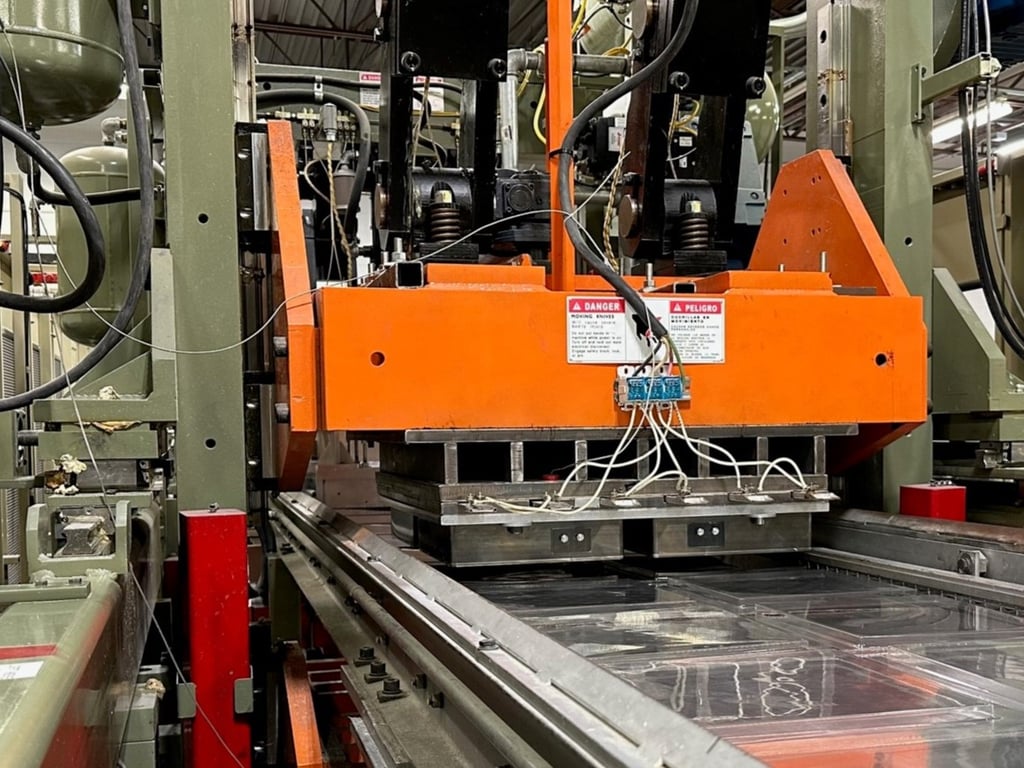
When a company comes to us with a tray project, one of the first things we want them to understand is the difference between thermoforming and injection molding. These are the two main manufacturing methods used to create plastic products like packaging trays.
Although they’re superficially similar — both reshape a raw thermoplastic to make a product — each technique has unique advantages that suit it best to certain types of projects. Injection molding tends to be best for large, thick, high-volume production runs. Thermoforming is faster, more cost-effective, and better for thinner-gauge products and more flexible production volumes.
Here are some insights into the more nuanced differences between these two processes.
Injection Molding vs. Thermoforming: What’s the Difference?
What Is Thermoforming?
A shaped plastic tray is created from a flat sheet of thermoplastic. The sheet is heated to make it pliable, then stretched onto a one-sided mold and formed into shape, either by creating a vacuum (vacuum forming) or applying positive pressure (pressure forming). After it cools and hardens, any excess material is trimmed off.
What Is Injection Molding?
The tray is made from melted-down and re-cooled thermoplastic beads. Hot, molten thermoplastic is injected into a two-sided mold at high pressure. Once it cools, the halves of the mold are separated and the finished plastic part is released.
Key Traits of Plastic Thermoforming vs. Injection Molding |
|
Thermoformed Trays |
Injection Molded Trays |
|
|
Tooling Costs
This is a significant point of difference, both in terms of cost and lead times. Thermoforming uses a single-sided packaging tray mold (a “form”) that can be made quickly from cost-efficient materials and can be rapidly CNC cut — great for custom projects. Injection molds are harder to make, requiring aluminum, steel, or copper alloys for a two-sided mold.
Raw Materials
Both processes use thermoplastics but in different shapes. Whereas thermoforming uses flat sheets, injection molds need pellets to melt. The same thermoplastic types will work in either process, and they can both produce tray packaging in various colors. Injection molding tends to use more raw material to complete a packaging tray of similar dimensions — especially when comparing thin-gauge trays.
Product Development Cycle
Tooling time for thermoformed packaging trays takes a matter of weeks, while injection molding will generally take three, four, or even more months before production can even begin. When it comes time to make your tray packaging, thermoforming can complete work at least twice as quickly, since injection molds must wait for liquid plastics inside of a mold to cool and harden.
Finishing Touches
Injection-molded trays are in the correct shape right out of the mold, whereas thermoformed trays must have the excess plastic at the edges of the sheet trimmed off to reach their final shape. However, injection molded items often need paint or another special coating before they’re presentable. Thermoforming makes a tray that’s ready for use as soon as it’s finished.
Overall Cost & Time
Between tooling, materials, production processes, and finishing, thermoforming is substantially more cost-effective and faster per part produced at low and medium volumes than injection molding.
Thermoforming vs. Injection Molding For Packaging Trays: Which Do I Need?
This will come down to the unique characteristics of the products you want to ship in the packaging trays. For most circumstances, thermoforming is your best bet.
Thermoformed packaging trays enjoy much faster production and lead times, lower tooling costs if adjustments or customizations are needed, and far lower prices per part. You’ll also have the flexibility to order in lower volumes if needed.
Injection molding can make sense for the right high-volume applications. If you’re shipping large volumes of products that are extremely heavy and bulk, an injection-molded tray might be ideal. These would be true outlier cases for tray packaging in most industries, given the high production costs for single-use packaging.
If you’re looking for high-quality, American-made thermoformed plastic trays, we’d love to work with you. Get in touch with the team at Ready Made Plastic Trays to discuss the needs of your project and we’ll get to work.