Why Do Manufacturers Choose Thermoform Plastic Trays For Shipping?
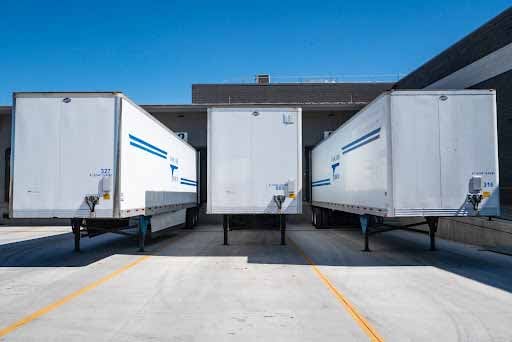
Molded plastic trays have grown in popularity among manufacturers across industries from medical to automotive to food and beverage. Between design flexibility, cost-efficiency, and durability, they’re ideal for organizing and delivering small or complex parts safely throughout the supply chain. But not all trays are alike. When it comes to production, there are two main methods for making them: injection molding and thermoforming.
Injection Molding and Thermoforming: What’s the Difference?
Injection molding involves melting plastic pellets and injecting the molten plastic into a mold under high pressure. Once the plastic has cooled and solidified, the mold is opened, and the finished product is ejected. Thermoforming, on the other hand, uses heat and vacuum pressure to form a sheet of plastic into a specific shape. The plastic sheet is heated until it becomes pliable, and then it is vacuum-formed over a mold to create the desired shape.
While each process has value, thermoform plastic trays are generally the preferred choice as a shipping solution for manufacturers. Here are the top five reasons why.
1. Design Flexibility: Bringing Your Vision to Life
One of the biggest advantages of thermoforming is the ability to create customized shapes and designs. Unlike injection molding, which is better suited for simpler shapes, thermoforming allows for a wide range of design possibilities, including complex multi-walled designs, undercuts, textures, and pockets in a variety of sizes and shapes including square, round, and rectangular.
Thermoforming also works well with a variety of plastics, so you can pick the perfect one for your product. We generally prefer high-impact polystyrene (HIPS) for its low cost and high strength. In contrast, injection molding requires expensive tooling to create a mold, which can be cost-prohibitive for small runs or custom designs. Since injection molding is better suited for simpler shapes, it’s less versatile in terms of design.
Whether you're looking for a tray with a unique shape or a special texture, thermoforming can bring your vision to life.
2. Cost-Effective and Sustainable Manufacturing
Thermoforming is a cost-effective and sustainable manufacturing method, especially for small runs. The upfront cost is lower because thermoforming molds are less expensive than injection molds. Tooling costs for large product tooling are substantially less and substantially faster with thermoforming than injection molds.
Thermoform plastic trays also give you the option to use recycled/recyclable base materials. Recyclability is just one aspect of the green story of plastics, however. According to research, plastics are usually the greenest material option. With thermoforming, you can get high-quality, recyclable plastic trays without breaking the bank or compromising on sustainability.
3. Fast Production Times: Get Your Trays Quickly
Time is money, and that's especially true in the world of manufacturing. Thermoforming has faster production times than injection molding, with minimal setup time. Whereas injection molding requires significant preparation (including the creation of a mold, which can take several weeks), thermoforming can begin immediately.
Prototypes of thermoform trays can be rapidly produced with CNC-cut wood tooling for quick access to sample trays. Trays can also be easily nested for efficient delivery in large quantities. Whether you’re looking for samples, stock options, or custom trays, you'll get your thermoformed plastic trays quickly and efficiently, without sacrificing quality.
4. Thin-Walled Parts: A Thermoforming Specialty
Thermoforming is well-suited to the production of parts with varying thicknesses, including thin walls — something that can be tricky to achieve with injection molding. If your product needs a tray with a thin wall, thermoforming is the way to go.
5. Intricate Designs with Precision and Detail
The thermoforming process allows for intricate designs with fine details, such as embossed logos or product information. Custom molded plastic trays can make use of this capability to help your products stand out and be clearly identified in warehouses or on the shelf. These details can be achieved with greater precision and accuracy than with injection molding, which will often result in blurred or less defined elements.
Thermoformed Trays for Your Manufacturing Business
If you're looking for a customizable, cost-effective, fast, and sustainable plastic tray, thermoforming is the way to go. With thermoforming, you can bring your vision to life with unique shapes and textures, get your trays quickly and efficiently, and help the environment. Plus, with the ability to produce thin-walled parts, thermoforming is a specialty that can elevate your products to the next level. So why wait? If you are looking for thermoformed plastic tray manufacturers, give Ready-Made Plastic Trays a call!