6 Things to Demand From Your Plastic Tray Manufacturer
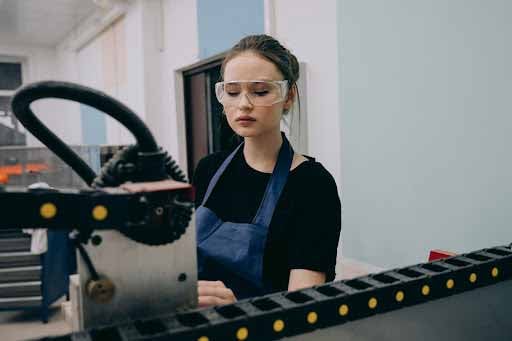
In today’s ultra-competitive market, the pressures of inflation and a still-unpredictable supply chain have companies searching for efficiency. It’s important to be aware of details as seemingly small as the standards and quality of your shipping solutions from plastic tray manufacturers.
The Most Important Items to Demand From Your Plastic Tray Manufacturer
A few things are non-negotiable when it comes to selecting a plastic tray manufacturer, including quality, fast lead times, superior service, and more. All parts delivered need to meet or exceed customer needs, whether you’re shipping low-tolerance medical parts or heavy-duty industrial components. Take a closer look below at the top six priorities for your shipping trays.
1. Traceability of Raw Materials
Traceability is critically important to guarantee that trays meet necessary quality and safety standards for the intended use, as well as to guarantee consistent performance and reliability.
You’ll want to be able to track any changes or updates to the raw material used in production to ensure sustainability goals are met and to ensure materials are legally and ethically sourced.
2. Exceptional Lead Times
Products should be consistently delivered on time and meet scheduling deadlines. When the manufacturing process is properly managed, it not only improves lead times but there’s less wastage of resources and materials — which saves money.
3. High-Quality Parts & Components
A high bar for quality from your plastic tray manufacturer ensures maximum performance, efficiency, and reliability. High-quality trays reduce wear and tear on products during shipping while also extending their life expectancy. High-grade materials, especially in sensitive use cases such as the medical industry, are necessary for peace of mind in the end product.
4. Customer Service
Demand excellent customer service from your plastic tray manufacturer, including timely delivery of orders, detailed tracking of items in transit, comprehensive communication about production timelines and potential delays or issues, and a responsible approach to environmental and safety regulations. Excellent customer service both reduces headaches and allows you to trust that you’ll achieve the best possible results for their customers.
5. Superior Manufacturing Standards
The products you purchase are a result of the standards set during manufacturing. To ensure customer compliance and satisfaction — as well as protect your brand reputation — it’s important to vet your tray manufacturer’s adherence to industry standards for materials and processes. This includes BPA-free trays for specific items, temperature control in production environments, and adequate testing to confirm material quality and strength.
6. Honesty & Integrity
These traits are essential for successful long-term partnerships. Businesses must be able to trust their suppliers to respect the confidentiality of any shared information. Honesty and integrity ensure that your business and your customers receive a consistent, safe product with no hidden surprises.
Work With a Quality Plastic Tray Manufacturer Today: Ready-Made Plastic Trays
Enterprises and businesses should always demand excellence and quality when working with a plastic tray manufacturer to create shipping trays that protect items and components.
Quality plastic trays ensure lasting performance, while those manufactured with subpar materials can lead to costly and time-consuming replacements or repairs. By partnering with an experienced and reliable plastic tray manufacturer, businesses can rest assured knowing they are getting top-notch products and services that meet their exact specifications.
With the right plastic tray manufacturer, companies can take advantage of higher quality trays that last longer, saving them time and money in the long run.
Don't wait any longer – Shop Now at Ready-Made Plastic Trays and partner with a reliable, quality plastic tray manufacturer today!